Experiences made to measure, sensory aesthetics, true sustainability. In the hospitality and contract world, interior design responds to increasingly stratified needs. A journey through Italy, Greece, Saudi Arabia, Iceland and the United Kingdom
Materially, the quest for new sustainable materials
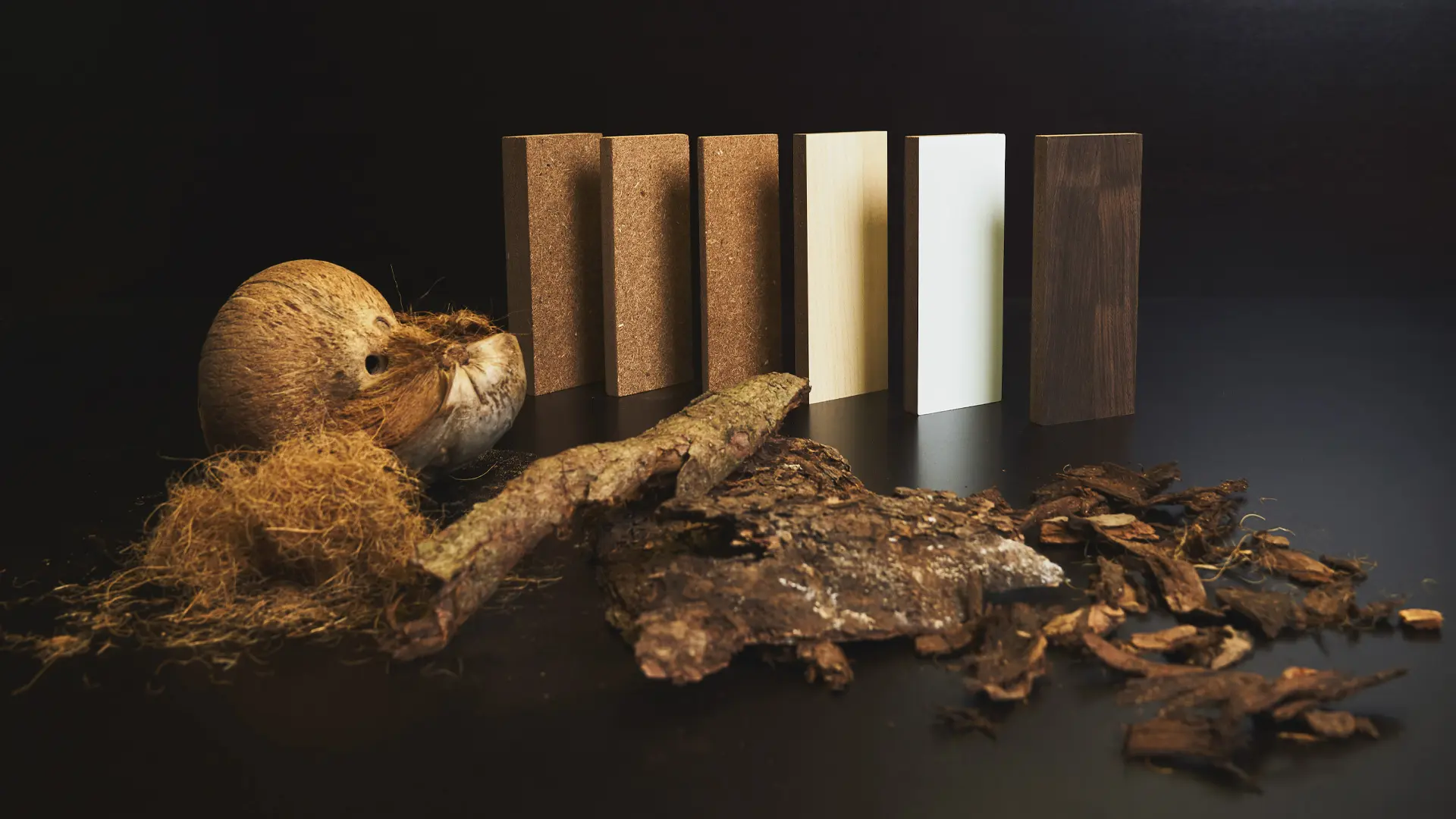
Cocoboard, coconut fiber panels, photo Naturloop
In conversation with Anna Pellizzari, Executive Director of Materially, a company that helps other companies innovate their products starting from materials
The choice of materials is one of the many design phases that can make an object more or less sustainable, but it is also the phase that most affects a product’s physical impacts on the environment. It’s a decision that inextricably binds together all the steps in a supply chain, from the primary resource to the finishing processes, until it becomes a knot to be untied at the end of the object’s lifespan. Telling us what is changing in the materials sector is Anna Pellizzari, for ten years CEO of Materially. “Materially is a company that works as a consultancy on the issues of innovation and sustainability of materials,” she explains. It is a partner of FLA-PLUS and together they are developing a digital library with the aim of helping companies in the wood-furniture sector to choose materials in a transversal way.
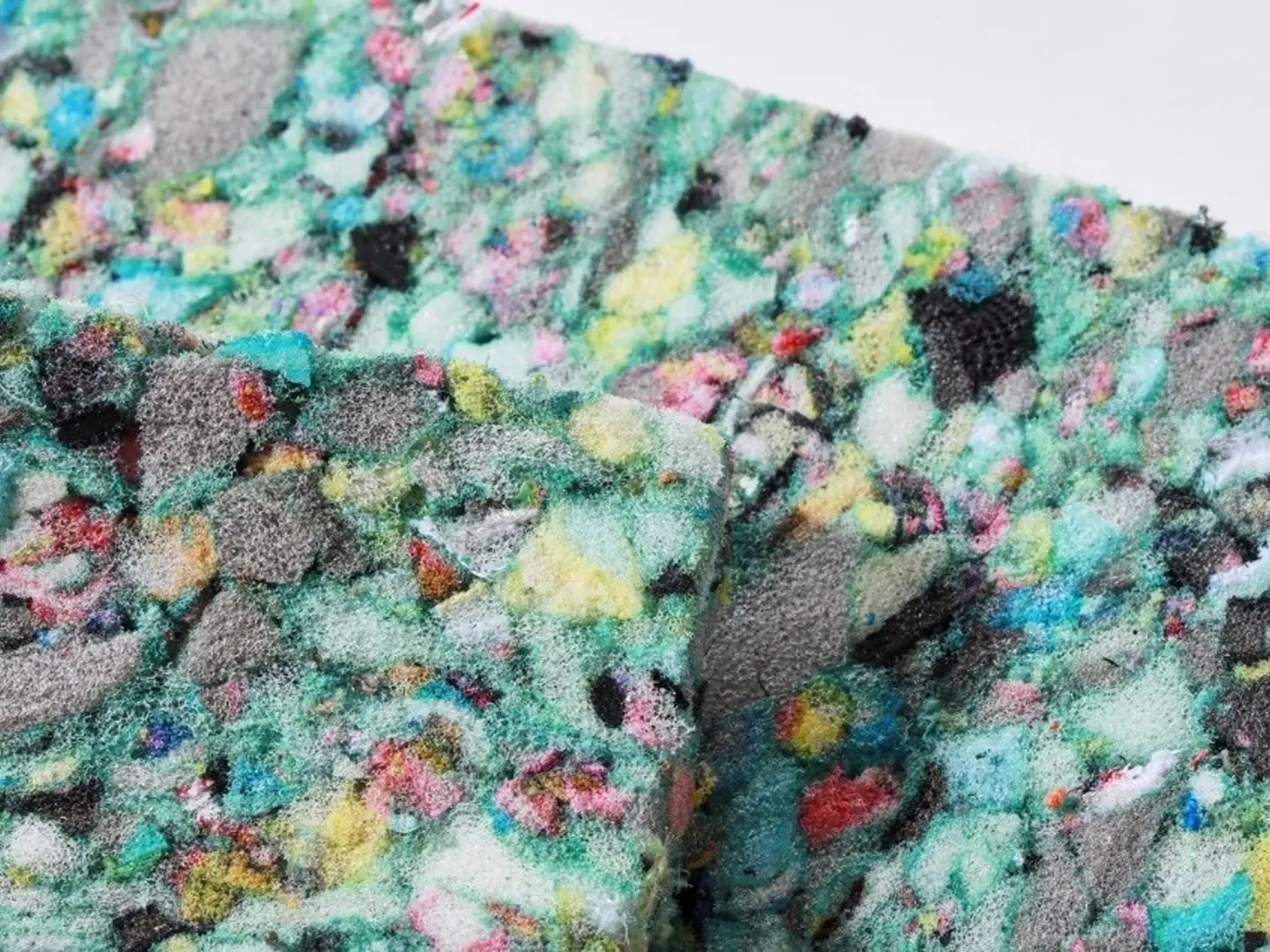
Recycled polyurethane panels, ph. courtesy Material ConneXion LLC
Sustainable materials
“The properties of sustainability, or rather the properties that reduce the environmental impact of materials have become a very important part of innovation in recent years. One of the mottos of Material ConneXion, a historic partner of Materially, is ‘design starting from the materials’, because a material often inspires an object, and companies are always looking for solutions in this respect, to be applied at different stages of the product’s development. Materially acts as an intermediary between those who produce innovative materials and those who use them. The former need to know whether what they produce has an application and in which market, while the latter are searching for ways to improve their products or ideas to produce something radically new. We work with virtually every industry, from packaging to retail, furniture, the automotive sector, sports and children’s items.”
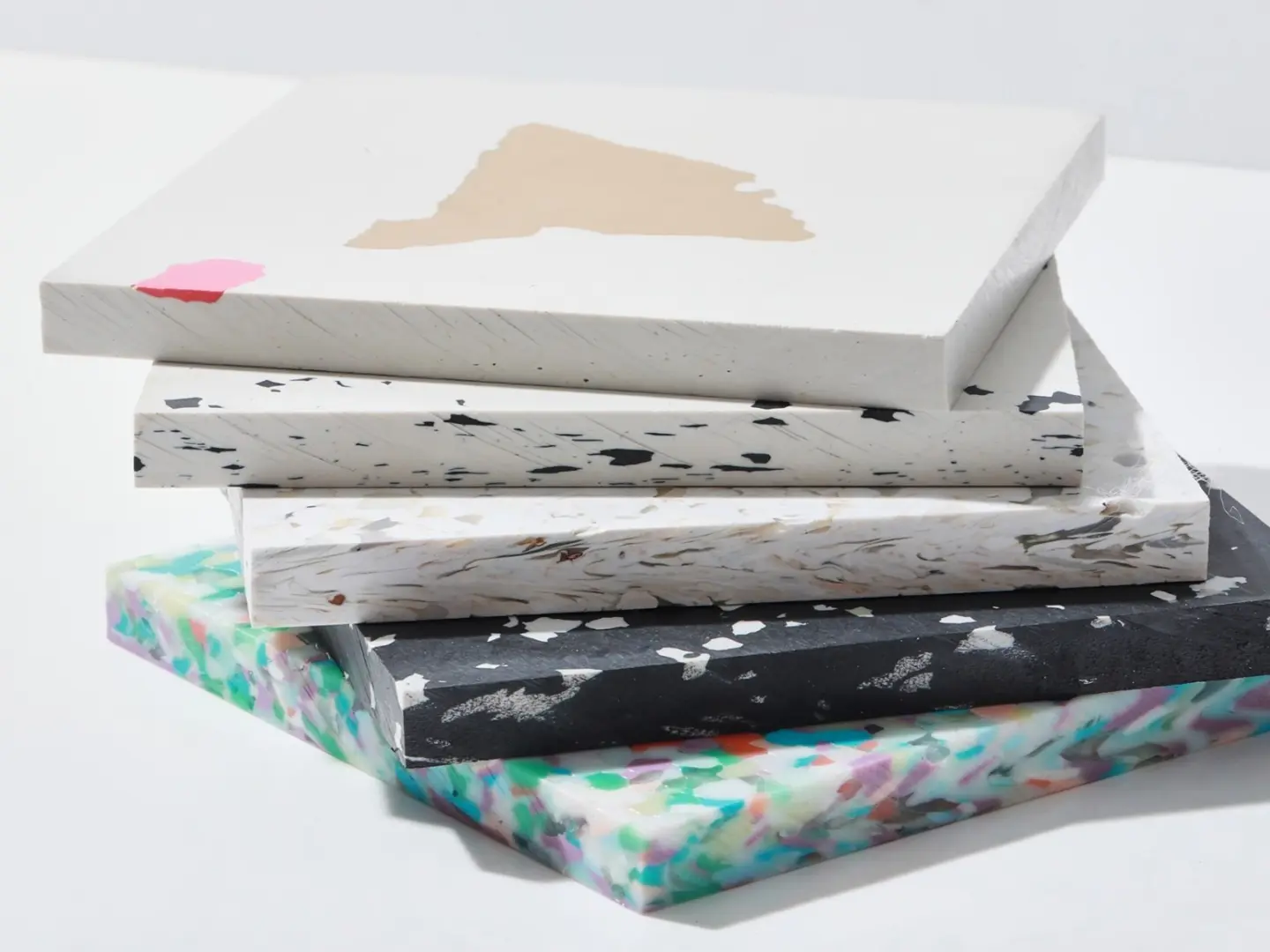
100% recycled plastic panels, ph. courtesy Material ConneXion LLC
Materials in the furniture sector
“With respect to sustainability, one of the central points of the wood-furniture sector – in my opinion already very virtuous because of the type of materials it uses – is the durability of the product. The Italian supply chain in particular is focused on durable products that the consumer can use for a very long time, so contributing positively to reducing the environmental impact of an object. Within the sector, in general, I trace three macro-types of approaches to circularity.
“The first approach is design for disassembling, a principle that, from the early stages, guides the design of objects that are easily dismantled: eliminating glues and adhesives, using joints and adopting all the solutions that allow easy replacement and repair of the components, so lengthening the product’s lifespan. This also simplifies end-of-life disassembly, which facilitates recycling.
“I call the second approach ‘systemic’. It intervenes in the processes and measurements of the company’s impacts with a substantial work of qualitative and quantitative analysis and with actions dealing with production as a whole. These include the use of renewable energies, the energy efficiency of processes, the elimination of pollutants, and much else.
“Finally, there is the approach centered on recycling and closing the circle of the material. It is a supply chain approach encompassing the whole world of recycled panels, and includes the main Italian players in the sector. These absorb the waste from the wood supply chain and recycle it to make panels to be reintroduced into the production cycle. “Examples of companies operating according to or one or more of these methods include Valcucine, which has built its product strategy on reduction and sustainability in the past; Flos, which since 2019 has been producing and designing new objects on the principle of design for disassembling; Arper, with its systemic approach to sustainability and impact measurement; and large panel manufacturers such as Fantoni, Saviola and Saib.
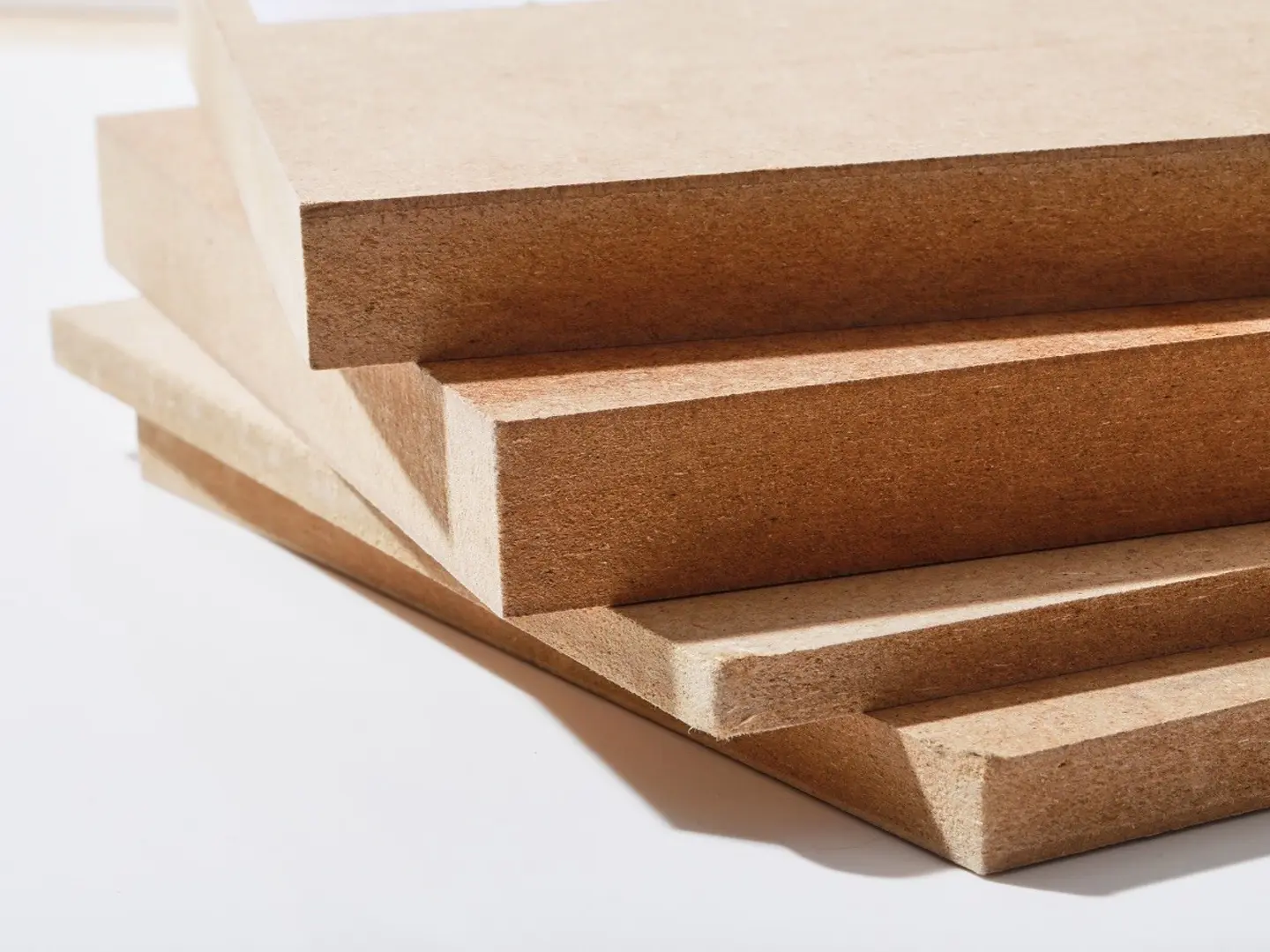
MDF panel with 100% bio-based certified binder, ph. courtesy Material ConneXion LLC
“With respect to sustainable innovation in individual materials, a hot topic is certainly padding, given the great demand (and search) for alternatives to polyurethane foam, a perfect material in terms of performance and durability, but not recyclable. Some companies are experimenting with natural fibers such as coconut or wood, others use single-component plastic foams. It should be said that a lot of work has also been done on the production process of polyurethane itself, acting on the system and the chemistry, greatly reducing its impacts.
“Another area where there are several innovative ideas is MDF replacement panels. In this sector we observe two main types of innovation. The first is the development of alternative binders to those based on urea-formaldehyde, from the need to reduce emissions during production of the panel and when it’s in use, as well as obtaining panels 100% from renewable sources. Here the semi-finished product remains as it is, but the resins that compose it change. The second method concerns the creation of completely different panels, starting from waste raw materials. On this subject, however, it would be appropriate to start a discussion on the possible emissions of these raw materials, which need to be measured, but also on their recycling. Often those who produce materials are more concerned with incoming raw materials and less with verifying that there exist supply chains capable of dealing with these new materials at the end of their life cycle. In this respect, an interesting example is panels that use recycled paper as their raw material, made only by using moisture and pressure without binders. Finally, there is the issue of ennobling. The raw panels in use have to be ennobled, which involves coupling them with different materials, often using synthetic glues, or painted. This complicates the material and makes it harder to assess its environmental impact.”
Materials and companies
This all goes to show that sustainable materials are extremely complex, but “I’m increasingly attracted by systemic approaches despite these complexities,” continues Anna Pellizzari. “In recent years we’ve seen very rapid and positive changes in the corporate culture on these issues. The companies we work with usually have their own inhouse R&D department, but an outside view is always useful, especially in getting out of their habitual mindset. Then in some cases innovation comes from other fields and what is needed is a bridge, an interlocutor with a broad vision and lateral thinking. At other times, however, very experienced companies are looking for new suppliers, but want to adopt different perspectives, so it’s easier for them to outsource the research.”

Photo Materially